Basic principle
Due to the applied torque, there is a relative displacement between the two slotted discs. Due to this relative displacement of the slotted discs, a phase shift exists between the pulse generated by the transducers. When these pulses are connected to an electronic unit, it will show a time lapse between the two pulses. This time lapse between the two pulses is proportional to the twist of the shaft and the torque of the shaft.
Description of Electrical Torsion Meter
1. The main parts of an electrical torsion meter are as follows:
2. A shaft connected between a driving engine and a driven load.
3. Two slotted discs attached on either side of the shaft.
4. Transducer (magnetic or photoelectric ) to count pulses from the slotted disc.
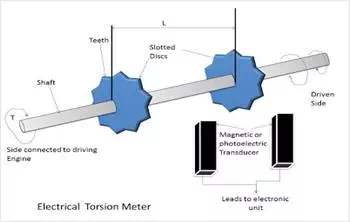
Operation of Electrical Torsion Meter
1. The teeth produce voltage pulses in the transducers.
2. When torque is not applied on the shaft, the teeth of the bth the discs perfectly align with each other and hence the voltage pulses produced in the transducers will have zero time difference.
3. But when torque is applied on the shaft, there is a relative displacement of the slotted discs due to twist experienced by the shaft and hence the teeth of both the discs will not align with each other and hence the voltage pulses produced in the transducer will have a time difference (that is , time lapse).
4. This time lapse between the pulses of the two discs is proportional to the twist of the shaft and hence the torque of the shaft.
5. A measure of this time lapse becames of torque when calibrated.
Application of Electrical Torsion Meter
1. Used to measure torque on rotating shafts.
Advantages of Electrical Torsion Meter
1. There are no signal leakage problems.
2. There is no noise creation.