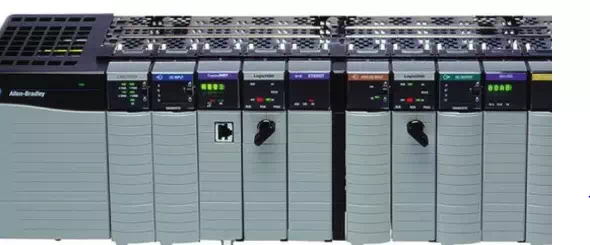
Allen Bradley’s Programmable Logic Controler (PLC) is one type of PLC that is widely used for industrial automation. There are 2 types of Allen Bradley PLCs, namely compact shapes and modular shapes. For compact forms, the PLC uses a rack system (CPU and I / O together) with limited memory capacity
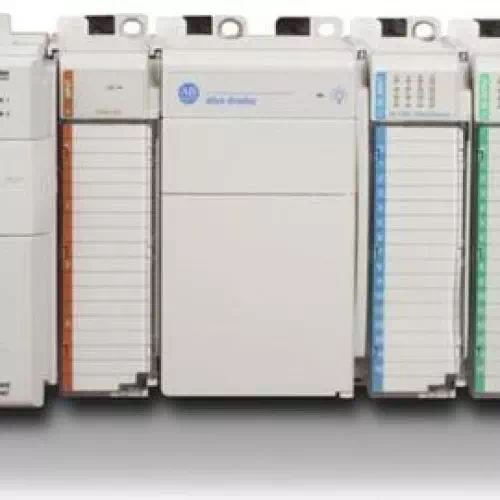
Whereas for PLC the modular form consists of a CPU module and an I / O module (a separate part).
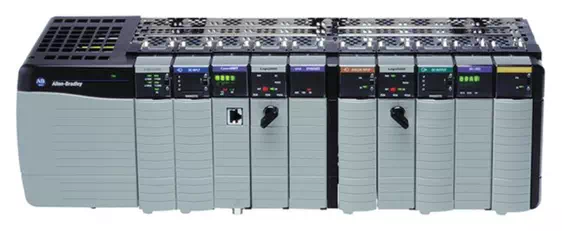
Allen Bradley PLC Module Modular Form
In one backplane there are 4, 7, 10 and 13 modules. The choice of backplane is adjusted to the needs, the more complex the system is made, the more backplane used. If more than 13 modules are needed, you must use an additional backplane because each backplane is up to 13 modules.
SLC 5/5 processor:
In one backplane there are 4, 7, 10 and 13 modules. The choice of backplane is adjusted to the needs, the more complex the system is made, the more backplane used. If more than 13 modules are needed, you must use an additional backplane because each backplane is up to 13 modules.
Analog Input (1746-N14):
This analog input module consists of 4 channels, input of each channel can be either dc voltage or dc current. To change the voltage or current input, a dip switch is located on the side of the module. In this type of module the voltage range is +/- 10 V while the current range is +/- 20 mA.
Analog Output (1746-NO41):
Like analog input modules, this module also consists of 4 channels but the output of each channel is only in the form of dc current with a range of 4mA – 20mA.
Digital Input (746-IB16):
The digital input module has 16 terminals. The input is a dc voltage with a range of 10-30 V. f. Digital.
Digital Output (1746-OW16):
The digital output module has 2 channels with 8 output terminals per channel. The output can be a dc voltage with a range of 5-125 V or an ac voltage with a range of 5-265 V.
RSLinx:
RSLinx is a software used for communication settings between PLC and PC.
RSView32:
RSView32 is one of the HMI software that allows monitoring of data in the field, in this case the data from sensors and tranducers in the field are controlled by the PLC.
RSLogix 500:
RSLogix is software that is used to create programs in the PLC. The ways that must be done to make a ladder diagram program using this software are as follows.
Programming Instructions:
These types of PLC programming instructions are:
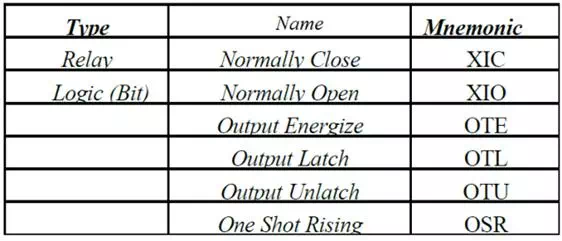
Timer:
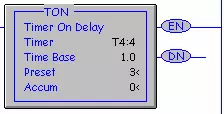
Timer on this type consists of Timer On Delay (TON) and Timer Off Delay (TOD). The address on the timer starts from T4: 00 to 39. This timer is equipped with bits consisting of EN (Timer Enable Bit), TT (Timer Timing Bit) and DN (Timer Done Bit).
Counter:
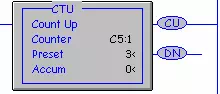
Counter consists of 2 parts namely CTU (Counter UP) and CTD (Counter Down). Symbol of CTU.
Reset (RES):
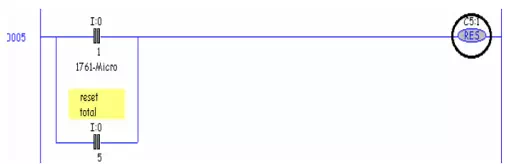
Used to reset the accum value of a counter until the value becomes zero (for CTU).
Add (ADD):
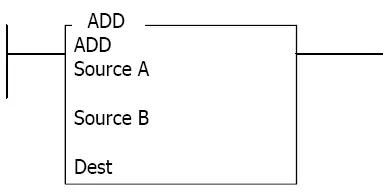
The value in source A is added to the value in source B and stored at Destination.
Move ( MOV ):
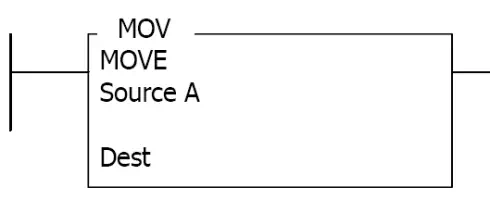
The processor copies the value on the source to the destination.
Jump to Subroutine (JSR):

If the condition for the space for the JSR instruction is true, then the processor will jump to the subroutine with the corresponding number
Subroutine (SBR):

The target of the subroutine is identified by the file number entered in the JSR instruction.
Return from Subroutine (RET):

This output instruction signifies the end of the subroutine or the end of subroutine execution so that scanning is continued to the space after the cell that calls this subroutine.